From the wiring in our homes, plumbing in our buildings, electronics in our devices to the coins in our pockets, Copper is omnipresent. Over the years, India’s relationship with copper has undergone a drastic change, from being a net exporter to a net importer.
What led to this situation? What went wrong with the copper Industry? How is this situation impacting the country’s growth?
Let us begin with understanding the geographical distribution of the Indian copper ore belts are and who owns them:
S.no | Copper Belt | State |
1 | Khetri belt | Rajasthan |
2 | Singbhum belt | Jharkhand |
3 | Malanjkhnad | Madhya Pradesh |
4 | Ingeldhal Mine | Karnataka |
- Copper ores are found mostly in Rajasthan, Madhya Pradesh, Jharkhand states.
- Hindustan Copper Limited owns most mines which include Khetri belt, singbhum belt, Malanjkhand and Ingeldhal mines.
- Copper Metal production plants is there only in two states namely, Gujarat and Tamil Nadu.
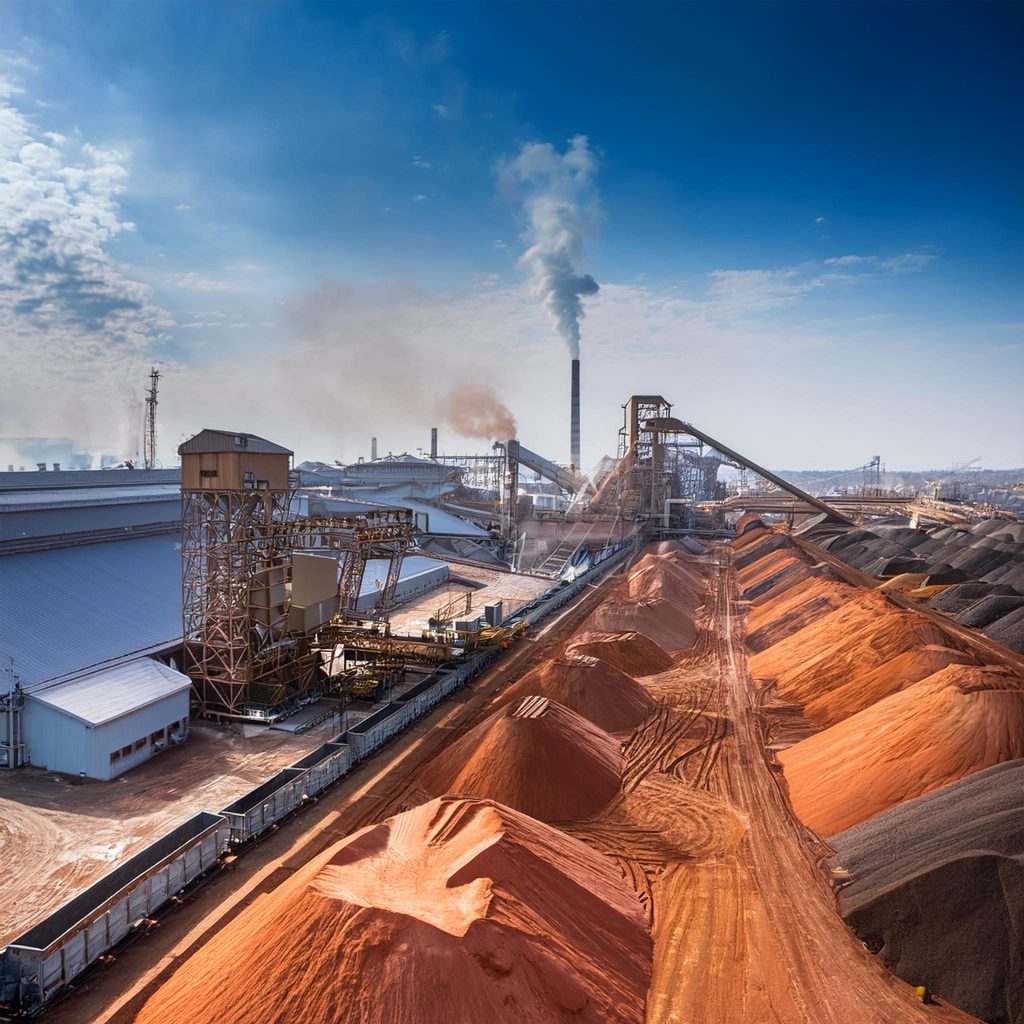
Mining production is just 0.2% of the world’s production, whereas refined copper production is about 4% of the world’s production.
What is Smelting?
Smelting is a process by which a metal is obtained from its ore by heating it beyond the melting point, in the presence of Oxidizing agents.
Till 1997, the only producer of primary refined copper in India was HCL (Hindustan Copper Limited). After economic liberalization, Sterlite Industries Ltd. (SIL) and Birla Copper (Hindalco Industries Ltd), started producing refined copper from imported & indigenous concentrates.
Hindustan copper limited (HCL) was the integrated company in the country involved in mining, smelting, refining and casting of refined copper.
Hindalco Industries Ltd and Vedanta Limited are the major copper producers in the private sector and mainly rely on imported copper concentrates. These companies own mines in other countries. Example: Vedanta owns a mine in Zambia.
Before analyzing the current situation, we need to understand the story that led to this situation.
Sterlite copper case:
Source: International Journal of Advances in Engineering and Management (IJAEM)
Sterlite copper is a subsidiary of Sterlite Industries, owned by Vedanta Limited. It was India’s largest copper smelter plant from 1988 to 2018. It encompassed not only smelter but also a refinery, a phosphoric acid plant and a sulphuric acid plant, fostering employment for approximately 1,500 individuals.
Sterlite copper had a global presence & was a public company. Despite having great industrial expertise, the plant faced a tough journey mired by controversies, leading up to its closure in 2018. The plant faced a lot of hatred and opposition from residents, mainly because of the concerns regarding environmental pollution and its impact on public health.
The origins of this case trace back to 1994 when Sterlite copper was founded in Tamil Nadu. It obtained the No Objection Certificate, but local opposition continued due to environmental and health worries, especially due to its location in a residential area.
However, construction commenced in 1995 & by 1997, despite protests, Sterlite copper was granted the necessary license to proceed by the government.
Reports from the National Environmental Engineering Research Institute highlighted violations of government regulations in ecologically sensitive areas. In 1999, a gas leak caused several people to be hospitalized and there were complaints about toxic water waste.
Madras High court ordered Sterlite plant to shut down its operations in 2010, due to legal violations but Supreme Court intervened and allowed Sterlite to continue its operations. Though the supreme court fined the plant up to Rs. 100 crores for environmental violations it allowed resumption of operations after a three-month shutdown.
Years passed with protests by residents while Sterlite plant continued its operations. Sterlite copper in the hope of business expansion wanted to increase its capacity to 800,000 Tonnes per annum by opening a second plant.
This is where the actual issues began; there was a huge protest that year. The Chief Minister also ordered its permanent closure because of the heavy pollution and its proposed expansion.
But Sterlite approached and appealed to the National green tribunal (NGT), which granted permission. Dissatisfied, Tamil Nadu government appealed to the Supreme Court, redirecting Vedanta to the Madras High Court. On August 18, 2020, the High Court dismissed Vedanta’s plea, affirming closure. The plant was permanently closed on that day.
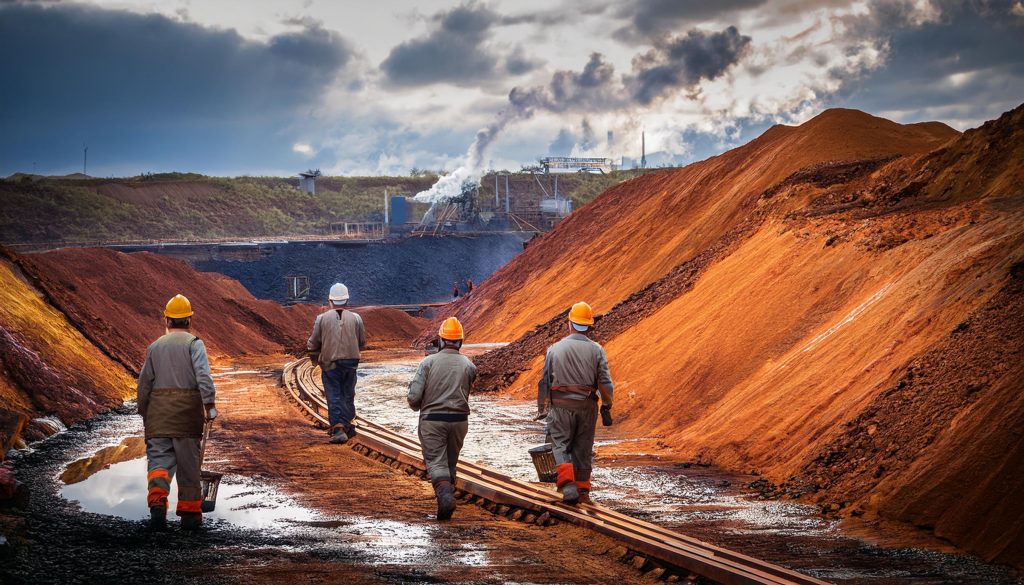
As per stats in 2017-18, Sterlite, which was owned by Vedanta, contributes to 40% of overall India’s copper production, Hindalco contributes 38% and Hindustan Copper contributes nearly 10%. Once the Sterlite plant was stopped, the production gap started. India was in dire need of copper and thus began the reliance on imports.
India became a net importer of copper for the first time in 18 years in 2018-19 with imports of refined copper shooting up to Rs 14,000 crore in that year.
According to the Ministry of Mines, the world copper production from April 2022 to March 2023 was about 22,052 thousand metric Tonnes (TMT). The share of India in the world production was 24.77 TMT i.e. 0.11% during April 2022 to March 2023.
Why do we need copper?
Copper is a metal which can conduct electricity and heat. The major use of copper is in electric circuits, wirings, and cables. The electric industry is the primary segment of application and accounts for about 35-40% of copper consumption.
Applications of copper:
Electric Vehicles: Irrespective of the manufacturer and battery technology used, the common material required is Copper. According to the report by IDTechEx, electric vehicles use considerably more copper than traditional vehicles with internal combustion engines.
- Internal Combustion Engine – 23kg of copper.
- Hybrid Electric Vehicle – 40kg of copper.
- Plug-in Hybrid Electric Vehicle (PHEV) – 60kg of copper.
- Battery Electric Vehicle – 83kg of copper.
- Hybrid Electric Bus (HEV) – 89 kg of copper.
According to a report by International Copper Mines, by 2027, an estimated 27 million electric vehicles (including HEV, PHEV, BEV, Ebus HEV and BEV) will be on the road, from a mere 3 million in 2017. This will raise copper demand in EVs from 185,000 Tonnes in 2017 to 1.74 million Tonnes in 2027.
Transport: Copper is used in cooling fans and water tubes for radiators and heaters in automobiles. Automobiles rely on copper motors, wiring connectors, brakes, and bearings. Copper and its alloys are used in all major forms of transportation. Copper nickel alloys are used on the hulls of boards and ships and other offshore structures to reduce marine biofouling, thereby reducing drag, and improving fuel consumption.
Building & Construction: In industrialized nations, significant amounts of copper are used in various forms like tubing, taps, valves, tanks, and fittings for building construction. These materials are valued for their durability and corrosion resistance.
Even in the manufacturing of the air conditioners, copper plays a key role. Copper is a crucial compoment, in the analysis of Blue star video, we explained how Air conditioner companies will face problem if there is no copper.
According to the Intenational Bureau of Mines report, the consumption of copper is as follows:
- Electrical Industry – 35%
- Transport – 11%
- Building – 8%
- Consumer durables – 8%
- Engineering – 8%
- Defense – 3%
- Others – 28%
The absence of copper production and reliance on imports would have significant negative impacts on the economy:
- Import Dependence: Without domestic copper production, India would heavily rely on imported copper to meet its industrial needs. This increased dependency on imports could lead to trade deficits and strain foreign exchange reserves. India spent Rs 27,131 crore on copper imports in 2022-23, up from Rs 21,985 crore a year earlier.
- Increased Costs: Importing copper could lead to higher production costs for industries reliant on copper, such as electronics, construction, and manufacturing. This could result in higher prices for consumers, reducing their purchasing power and impacting overall demand.
- Supply Chain Disruptions: Industries that rely on copper, including electrical, electronics, and automotive sectors, may face supply chain disruptions due to reliance on imported copper. This could lead to delays in production, affecting economic productivity and growth.
- Infrastructure Development: Copper is essential for infrastructure development, including power generation, transmission, and telecommunications. Without domestic production, there could be constraints on infrastructure expansion and modernization efforts, hindering economic growth and development.
- Technological Innovation: Copper is vital for technological innovation, particularly in renewable energy and electric vehicles. The absence of domestic production may impede technological advancements and competitiveness in these sectors, affecting long-term economic sustainability.
What is the Indian Government and the India Inc. doing to tackle the Copper issue?
The Ministry of Mines has proposed sending an Indian industry delegation to copper-rich Zambia to discuss potential copper exploration and mining projects in the southern African country.
Why Zambia?
With approximately 6 percent of the world’s copper reserves nestled within its borders, Zambia shines as the eighth-largest copper producer in world as of 2022. While India has a modest presence in Zambia in general, it has already established a foothold in Zambia’s vibrant copper mining landscape.
The Ministry of Mines is spearheading an initiative to foster closer collaboration between India and Zambia through a joint business delegation comprising representatives from both the private and public sectors. Among the eager participants seeking to explore mining opportunities in Zambia is Hindustan Zinc, a subsidiary of Vedanta Limited. Notably, the Indian government holds a substantial 35 percent stake in Hindustan Zinc, underscoring the shared interests between the public and private sectors.
The Adani Factor
The Adani Group is building the world’s largest single-location copper manufacturing plant at Mundra in Gujarat.
Kutch copper Ltd, a subsidiary of Adani Enterprises Ltd, will set up a copper refinery for the production of 1 million Tonnes per annum capacity of refined copper in two phases. The $1.2 billion facility, which will start operations by March end, aims to produce 0.5 million Tonnes of copper in the first phase.
Adani Copper’s operations could contribute to increasing India’s domestic copper supply and help reduce the country’s reliance on imported copper, thus enhancing energy security, reducing the trade deficit, and also making India a net exporter.
Copper demand in India has surged by 16 percent to 15.22 lakh Tonnes in 2023 from 13.11 lakh Tonnes in 2022. If Adani starts producing 1 million Tonnes it will supply more than 66% of Indian needs, whereas the other producers, namely Hindalco and Hindustan Copper Ltd could make up for the rest. Sterlite copper is also planning to expand its production. If the things happen in the way they are planned, India soon can become the net exporter again.
This analysis was covered in video format, if you want to watch the video, check out the video in our youtube channel
Conclusion
This Industrial growth will propel economic growth and create employment opportunities but adherence to the environmental laws, sensitivity to the community & good corporate governance is mandatory for success of this industry.
If there is a failure to bolster copper production, then, India needs to rely on copper imports, which will increase the costs of all the products that need copper. Domestic production would be a great win for the economy, India Inc. & the Indian consumers who will have to shell down less for goods that matter!
Savart is a SEBI registered investment advisor. The purpose of this content is to educate & not advise/recommend any particular security. Investments are subject to market risks. Please conduct thorough due diligence or seek professional guidance before making any investment.